Understanding Porosity in Welding: Discovering Reasons, Impacts, and Avoidance Methods
As professionals in the welding market are well conscious, comprehending the causes, impacts, and avoidance methods associated to porosity is crucial for accomplishing durable and reputable welds. By delving right into the origin causes of porosity, analyzing its detrimental effects on weld high quality, and discovering reliable avoidance methods, welders can boost their understanding and abilities to generate high-grade welds consistently.
Common Causes of Porosity
Porosity in welding is mostly brought on by a mix of variables such as contamination, improper protecting, and insufficient gas protection during the welding process. Contamination, in the kind of dust, oil, or corrosion on the welding surface area, creates gas pockets when heated up, resulting in porosity in the weld. Inappropriate shielding happens when the protecting gas, generally used in processes like MIG and TIG welding, is unable to fully shield the liquified weld pool from responding with the bordering air, causing gas entrapment and subsequent porosity. Furthermore, poor gas insurance coverage, frequently as a result of wrong circulation rates or nozzle positioning, can leave parts of the weld unguarded, enabling porosity to form. These aspects collectively add to the formation of gaps within the weld, deteriorating its stability and possibly triggering structural concerns. Comprehending and resolving these typical causes are vital actions in avoiding porosity and making certain the top quality and stamina of welded joints.
Impacts on Weld Top Quality
The existence of porosity in a weld can dramatically endanger the total top quality and integrity of the bonded joint. Porosity within a weld creates voids or tooth cavities that damage the framework, making it a lot more vulnerable to cracking, corrosion, and mechanical failing.
Moreover, porosity can impede the effectiveness of non-destructive screening (NDT) methods, making it challenging to spot other defects or suspensions within the weld. This can bring about significant safety worries, specifically in crucial applications where the structural stability of the bonded parts is paramount.
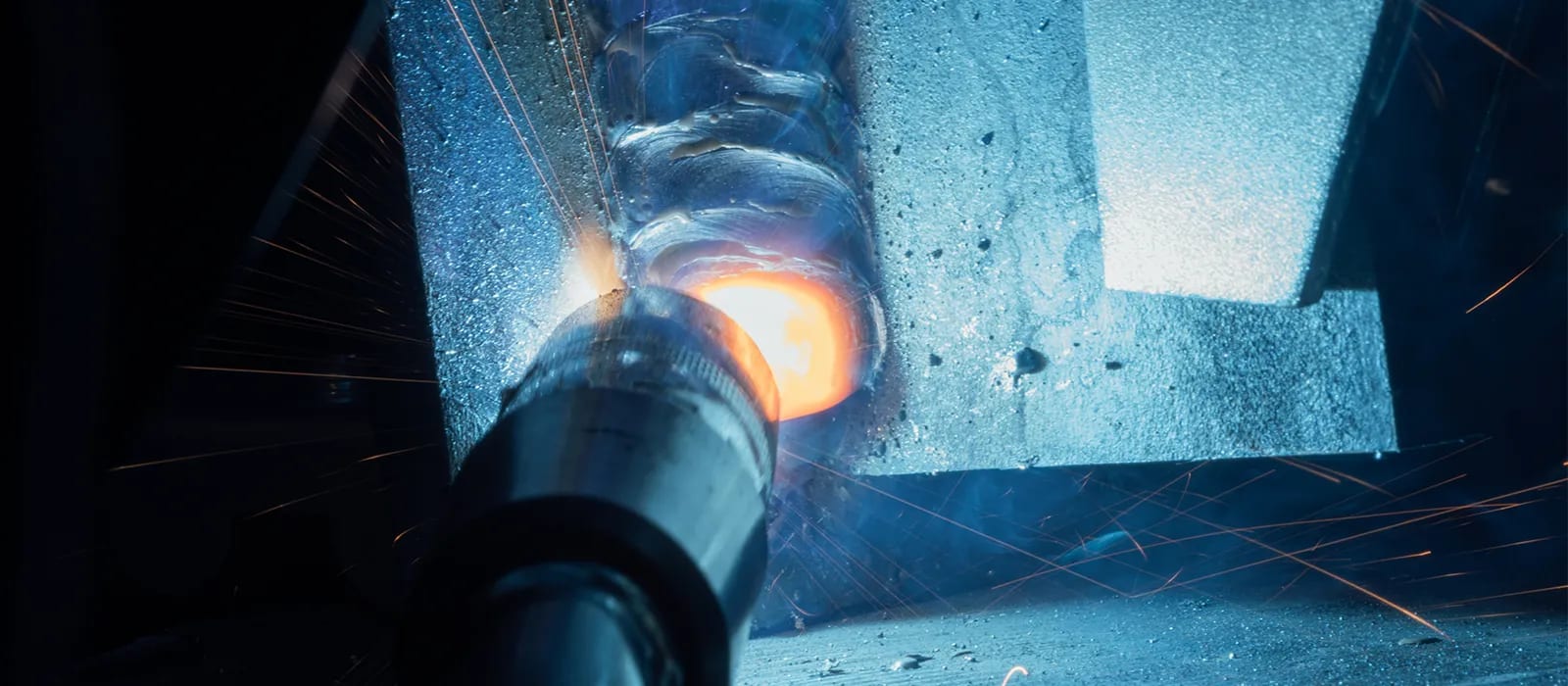
Prevention Techniques Overview
Provided the harmful effect of porosity on weld quality, effective prevention techniques are vital to maintaining the structural honesty of bonded joints. Among the main avoidance strategies is thorough cleansing of the base products before welding. Pollutants such as oil, grease, corrosion, and dampness can add to porosity, so ensuring a tidy job surface is crucial. Proper storage of welding consumables in dry conditions is also important to stop wetness absorption, which can lead to gas entrapment throughout welding. Additionally, selecting the appropriate welding criteria, such as voltage, current, and travel speed, can aid reduce the risk of porosity More Info formation. Making sure appropriate securing gas flow and protection is another crucial avoidance method, as insufficient gas insurance coverage can lead to atmospheric contamination and porosity. Finally, correct welder training and accreditation are important for applying precautionary measures efficiently and consistently. By integrating these avoidance techniques right into welding methods, the event of porosity can be considerably reduced, leading to stronger and more reliable welded joints.
Value of Correct Shielding
Correct shielding in welding plays an important function in avoiding atmospheric contamination and making certain the stability of bonded joints. Protecting gases, such as argon, helium, or a blend of both, are typically made use of to secure the weld pool from responding with components in the air like oxygen and nitrogen. When these responsive elements enter call with the hot weld pool, they can trigger porosity, resulting in weak welds with lowered mechanical buildings.
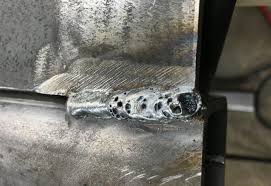
Inadequate securing can result in different flaws like porosity, spatter, and oxidation, jeopardizing the structural stability of the bonded joint. Adhering to correct protecting practices is important to produce top quality welds with marginal flaws and ensure the longevity and integrity of the welded parts.
Tracking and Control Methods
Exactly how can welders successfully check and regulate the welding procedure to guarantee optimum outcomes and avoid flaws like porosity? By constantly keeping an eye on these variables, welders can recognize variances from the suitable problems and make immediate changes to stop porosity formation.

In addition, executing appropriate training programs for welders is crucial for monitoring and regulating the welding process successfully. What is Porosity. Enlightening welders on the relevance of maintaining regular parameters, such as proper gas shielding and travel speed, can assist stop porosity concerns. Normal evaluations and certifications can likewise make sure that welders excel in tracking and managing welding processes
Moreover, making use of automated welding systems can enhance tracking and control abilities. These systems can specifically manage welding criteria, lowering the chance of human error and making certain consistent weld top quality. By incorporating innovative surveillance innovations, training programs, and automated systems, welders can properly monitor and control the welding procedure to decrease porosity flaws and attain premium welds.
Final Thought
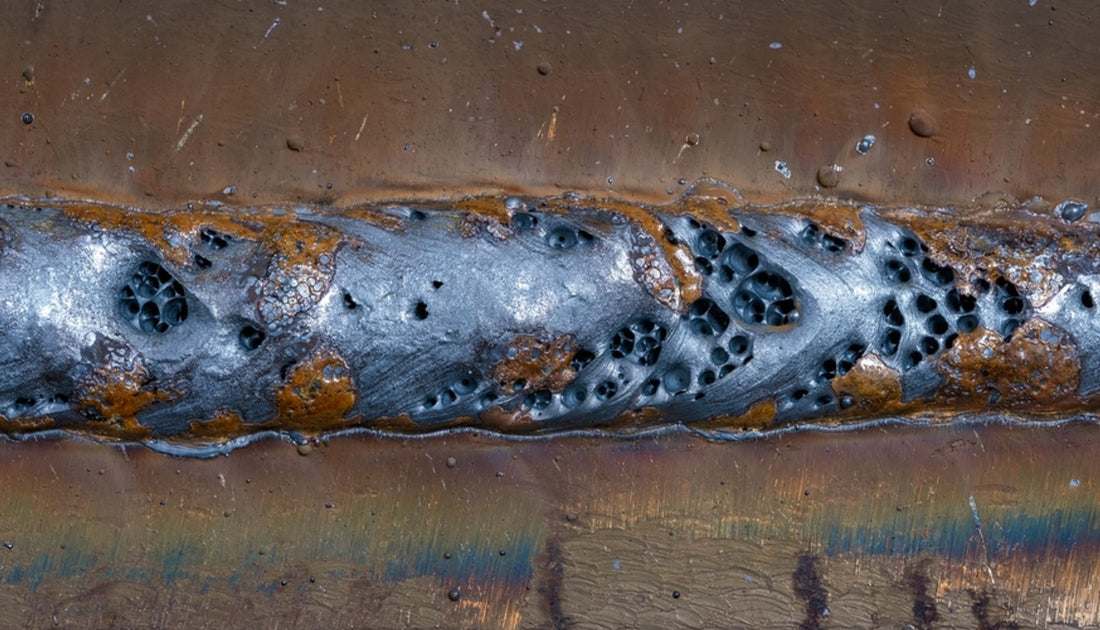
Comments on “What is Porosity in Welding: Ideal Practices for Staying Clear Of Porous Welds”